What are Pre- & Post-Treatment? – PVD Coatings Part IV
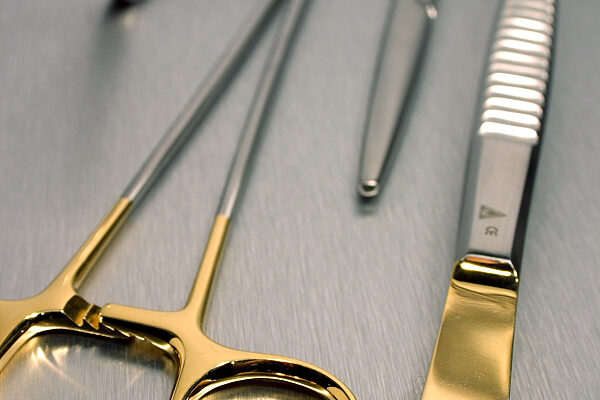
To increase the quality and longevity of a part’s external coating, pre-and post-treatment are essential to the process. A PVD coating is only as successful as the thoroughness of each process step. Post coating use or the “application” is only part of the equation. An excellent coating provider partner will also strive to understand your manufacturing process so the proper steps are completed to ensure peak performance.
Pre- and post-treatment of the part is simply the due diligence of a quality PVD coating provider.
Pre-Treatment Explained
Pretreatment is necessary to remove adhesion inhibitors of three types – oils, particles, and oxides. The manufacturing process of your part from parent material selection, grinding, wire EDM, machining, heat treat, passivation, polishing, all have a unique effect on the surface incredibly important from a Tribological perspective. Correct pretreatment takes these steps into consideration to maximize your coating adhesion. Some of these steps are done by the customer and some by your coater. Your steps have a direct influence on ours.
Here are a few key points to better understand the necessity of coating pre-treatment:
- Premature polishing covers up defects (occlusions) and embeds debris.
- Debris needs to be removed, not just smoothed over.
- Blasting can create a problem by embedding grit on a surface. Always use clean media at an oblique angle and a distance proportionate to the material, grit, and pressure. Blow a tool free of media including holes front and back.
- Note that a blasted surface will need to be lightly oiled to prevent rusting. As an oxide, rust will ruin your finish and coating.
- It’s best to not start polishing until you have a 100 grit, ground finish, or better
- Sometimes it is best to leave your parts in the lubricant it was made with. A qualified coater will ensure your part is cleaned thoroughly and properly prior to coating.
Pre-treatments available include but are not limited to traditional polishing, surface asperity removal, oxide, and scale removal, deburring, stone finishes, diffusion layers for increased toughness and hardness, and honing for different material cutting. Every application and every material substrate has a key for optimal performance. Our experience gets you there. Some of it is basic, no worries, sometimes it requires a bit of a deeper look by a professional coating team that cares about your performance.
Post-Treatment Explained
Post-treatments following coatings are mostly for the removal of macroparticles from a well adhered PVD coating applied to your part. If adhesion is strong and your surface was polished you will see nearly identical finishes pre and post-coating.
The purpose is to remove any lingering asperities on the surface. Some surfaces require directional surface modifications that are easy to achieve. If roughness is an issue, it can be addressed. No coater wants their customer in a position that requires a diamond polish. This can significantly remove coating thickness, even in critical working areas, where done manually the “feel” of the part is better but its performance may be diminished. Open and transparent communication with your PVD supplier is necessary to reach any specific part requirements.
Post-treatments available include but are not limited to macro particle removal – an alternative to traditional post-coating polishes which remove coating thickness and compromise the adhesion of the coating and integrity; Teflon-based lubricants; and dry film lubricants.
Customized Coatings
Let DCT show you how to improve your part’s performance. We have the technology and methods – with an experienced team to back them up – that result in reputable, repeatable solutions. Our team will implement steps to make you a better product.
[…] further reading, check out our Part IV of getting to know PVD […]