A Clean Surface Is Critical – PVD Coatings Part III
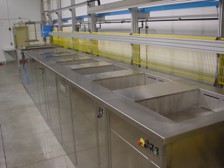
Part III to PVD Coatings brings us to gain a deeper understanding of PVD coatings and how the manufacturing process could result in an undesirable surface to coat.
As an educated customer, you will save time and money by having a base understanding to choose an experienced PVD provider. With a quality PVD provider, you will have peace of mind knowing they will ensure properly cleaned and inspected parts designed for sustainability.
Oxides & Adhesion Inhibitors
Like we discussed in Part II, different manufacturing methods such as EDM, grinding, and machining generates heat that can leave trace thin lines of oxide that will not allow the coating to stick. When a metal part is manufactured, the process involves lubricants, oils, and oxides, which PVD coatings will not adhere to in the slightest.
Additionally, certain materials like cobalt are a challenge as they are both a binder to the tungsten and an adhesion inhibitor to the PVD coating when unbound and on the surface, i.e. a cobalt enriched surface. Wire EDM creates a nitride that also blocks coating adhesion if not removed properly; similarly, pH and temperatures from a high range will leave behind oxides that need to be removed. Rust is another oxide that will ruin your finish and coating.
Fortunately, many types of processes exist to handle these challenges. A proven process for the removal of lubricants and hydrocarbons is an aqueous cleaning line. But to remove oxides, your parts have to be machined or worked on to physically remove the oxide. Not as simple as washing it off.
You would be surprised how quickly a passivation process, temp or pH, radically affect a part’s corrosion resistance after PVD coating. Controlling passivation better is direct cost savings for customers both in-house and at your coating house.
Pro Tip: Ask your coating specialist to thoroughly inspect your parts’ surfaces for burrs and oxides before pre-treatment. Experts will have that detailed eye to ensure coating success. Ask us about the most common sneaky places these built-in defects hide.
Questions to Ask Your Coating Specialist
- Are they counting and inspecting each individual part?
- Do they have trained technicians or tray handlers?
- Are they cleaning all the tools collectively in a single dishwasher-style system?
- Does your coater take the time to understand your process? Every manufacturing process is unique and requires different treatments by your coater to ensure perfect adhesion.
Pro Tip: Quality coating companies will finish parts per a specification like ASTM A380 or AMS 2444 to ensure tool surfaces are acceptable for PVD coating.
Ultimately, it is best to not start polishing until all adhesion inhibitors (i.e., scale and oxides) have been removed. Your polisher will then need to bring the surface up gradually using stones; followed by specialized paper; and completed with a polishing compound. This allows for an optimal smooth surface for coatings to adhere to. And limits the possibility of oxides being polished into the surface, creating stress on your part which will prevent coatings from adhering.
The cleaning process should be easy with an experienced coating specialist. Your coating partner will understand the necessity of a clean surface for your bottom line. Many different types of pre-and post-treatment are available. Follow us along to Part IV to learn more about the treatment process.
Customer Success Guaranteed
After 20+ years of improving customers’ performance and our own product line, we operate a winning company that is hyper-focused on service. With an exceptional team of professionals, DCT only uses world-class technology to guarantee mutual success. Contact us to get started!