Titanium Nitride (TiN)
This general-purpose coating is gold in color. The Titanium Nitride PVD Coating is great for cutting, forming and injection molding. Not only that, but it is also a great tribological coating for other various applications, as well.
The Titanium Nitride PVD Coating is a hard-ceramic material. It is used to coat a product’s surface, essentially increasing the lifespan or improving the function of the product. The TiN PVD coating has excellent hardness and toughness, along with reduced friction. TiN coatings contain an inert and stable material, with very firm adhesion. This is, ultimately, due to a molecular bond to the substrate metal. Furthermore, it is biocompatible and even non-toxic.
The application of the Titanium Nitride layers will be precisely implemented, in accordance with PVD technology. This means that the deposition of the coating layer can operate at a temperature of 800°F. The TiN coating is thoroughly applied using physical vapor deposition vacuum systems, or otherwise known as PVD Coating equipment.
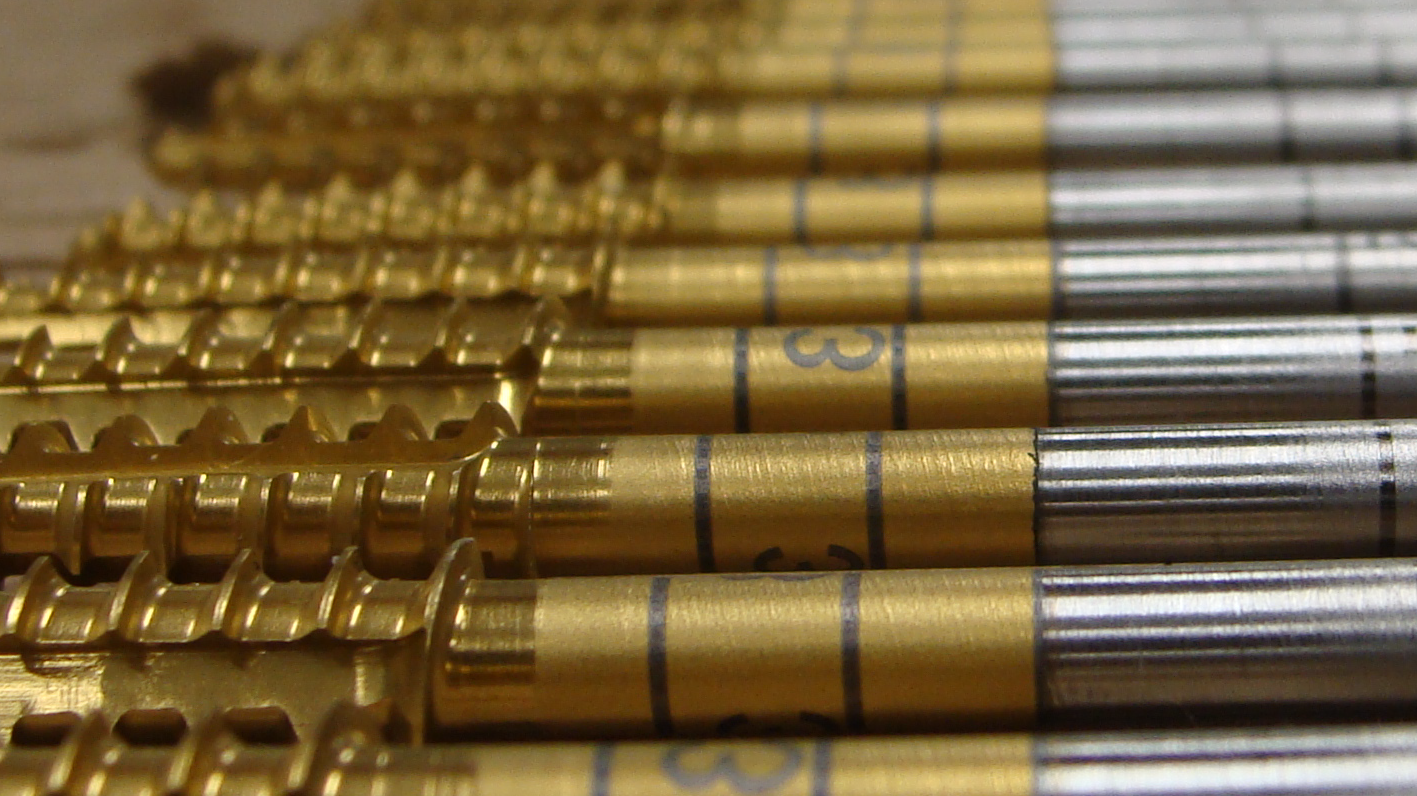
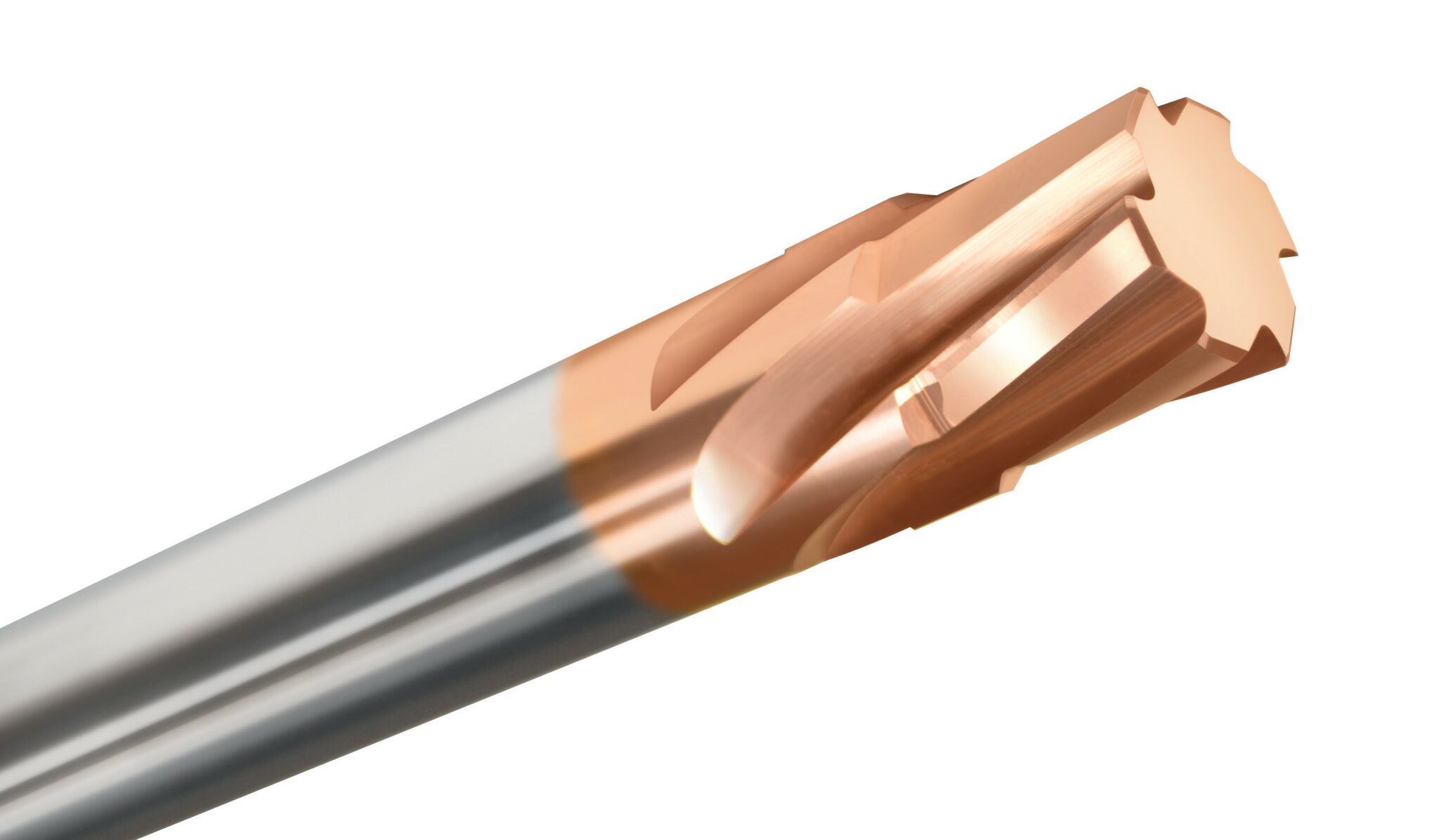
Titanium Carbon Nitride (TiCN)
Titanium-Carbon Nitride (TiCN) is a PVD Coating with a rose-gold color.
The TiCN coating has hard-ceramic material, used to thoroughly coat the surface of a product. This titanium-carbon nitride coating has the ability to successfully increase the lifespan or function of a specific product, as well. The proprietary process of the TiCN coating ensures excellent adhesin, with consistency in thickness and surface control. In addition, the carbon in the morphological structure of the TiCN coating can reduce friction coefficients dramatically.
A TiCN PVD coating is deposited on a product’s surface with the use of PVD technology. These coating layers can be deposited on tool steels, HSS, cemented carbides and many other materials. It is necessary that a TiCN coated product receives the accurate heat treat and surface finish methods. The TiCN coating has one of the lower melting temperatures of the PVD coating options. Coating a component with this PVD Coating will require a temperature that is under 800°F.
Zirconium Nitride (ZrN)
Zirconium Nitride (ZrN) is a general-purpose coating that has a pale gold color to it. A ZrN coating has excellent corrosion resistance, as well as great abrasion resistance. This coating is going to provide your product with extreme hardness and toughness. Not only that, it is additionally biocompatible, successfully meeting all of the biocompatibility requirements.
Due to the coating's corrosion resistance and chemical stability, ZrN can be used for medical components that will come into direct contact with bones, skin, tissue or even blood. The improved ZrN coating is, especially, suitable for the machining of aluminum alloys (Al/Ti). It is, also, a good choice for machining non ferrous metals, specifically with cutting and punching tools. Furthermore, this PVD Coating is highly recommended for machining fiberglass, nylon and the majority of polymer materials.
Common Applications With The Zirconium Nitride PVD Coating:
- Cutting | General high performance cutting operations
- Stamping & Forming | For applications that lead to cold welding
- Decorative Applications | Effectively protects against abrasive and adhesive wear
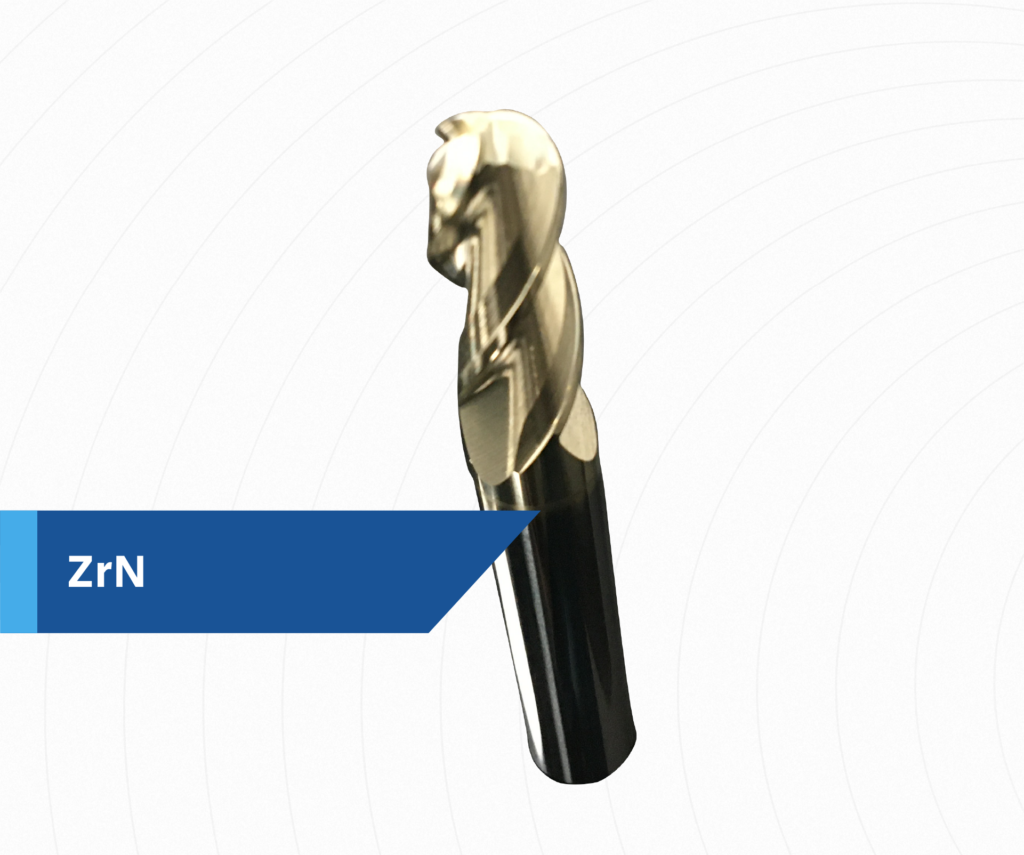
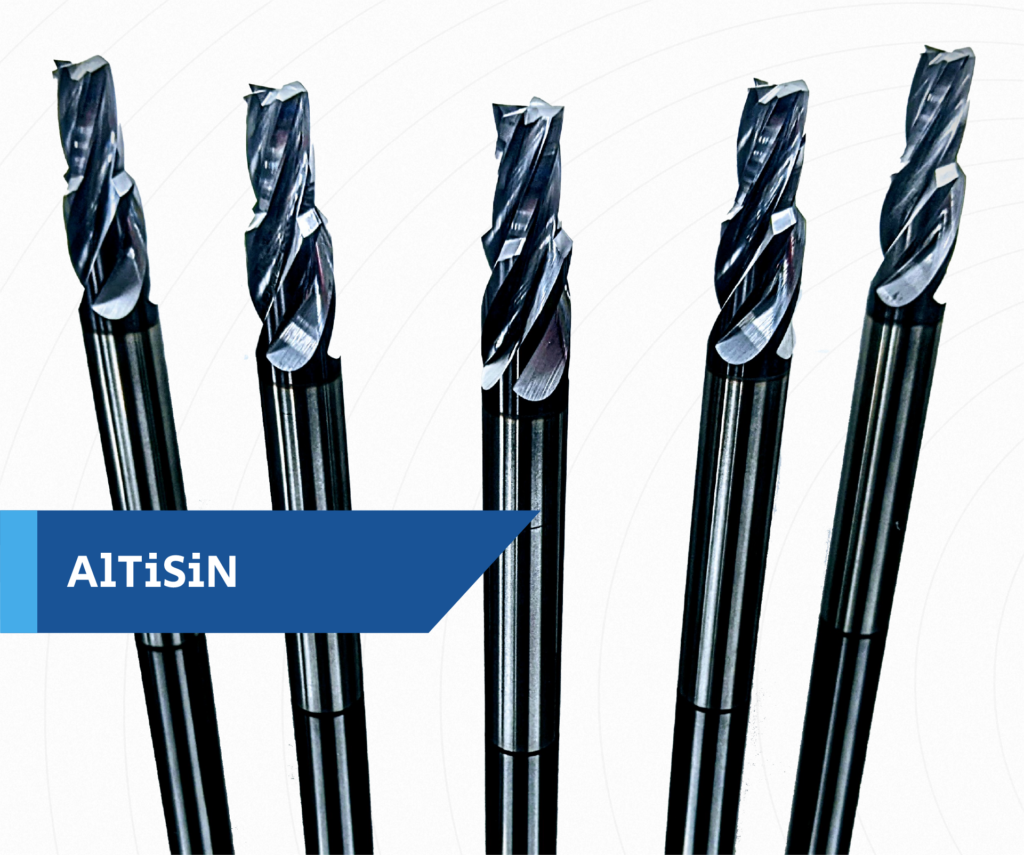
Aluminum Titanium Silicon Nitride (AlTiSiN)
AlTiSiN has been developed more recently, grouped with a new breed of nanocomposite materials. However, TiN is still the foundation of this PVD Coating, but with some additional Al and Si elements. The outcome will result in a super-hard coating, with outstanding toughness, along with a hot-hardness that exceeds 1800°F. With a proper deposition procedure, the microstructure of this elite coating will consist of dispersed AlTiN hard particles, among a Silicon matrix.
An Aluminum Titanium Silicon Nitride (AlTiSiN) PVD Coating has good oxidation resistance. This particular coating can maintain mechanical properties at a high temperature. Ultimately, this is going to be extremely important to the surface protection of high speed machining or hot forming tooling parts.
The AlTiSiN coating is composed of nano-crystalline, a TiN inter-layer and Silicon. This PVD Coating is particularly known as a hard coating matrix, with high physical and mechanical properties, high oxidation resistance and a high thermal stability.
Aluminum Titanium Nitride (AlTiN) | Titanium Aluminum Nitride (TiAlN)
Aluminum Titanium Nitride (AlTiN), or Titanium Aluminum Nitride (TiAlN), is known as a dark grey coating color. This coating is normally applied to steels, hardened steels, and stainless steel materials, essentially where high wear resistance and lubricity are needed. The TiAlN PVD coating will provide exceptional oxidation resistance and extreme hardness. This coating is regarded as the new universal and high-performance coating. It is highly suitable for dry machining, as well as cutting operations.
- Drilling
- Milling
- Reaming
- Turning
A TiAlN coating is going to provide high temperature resistance, especially when compared to the TiN PVD coating. It is primarily utilized in an environment that has extremely high temperatures. This is, ultimately, due to the higher hardness that this particular coating contains. The slightly higher hardness of the coating will ensure that your product effectively handles higher temperatures, with extreme environments. These higher temperatures can, essentially, rise way above the limits of a TiN coated product.
Titanium Aluminum Nitride (TiAlN) is a hard coating that will solve many tribological problems, especially with components that can be coated at temperatures ranging from 842°F - 887°F.
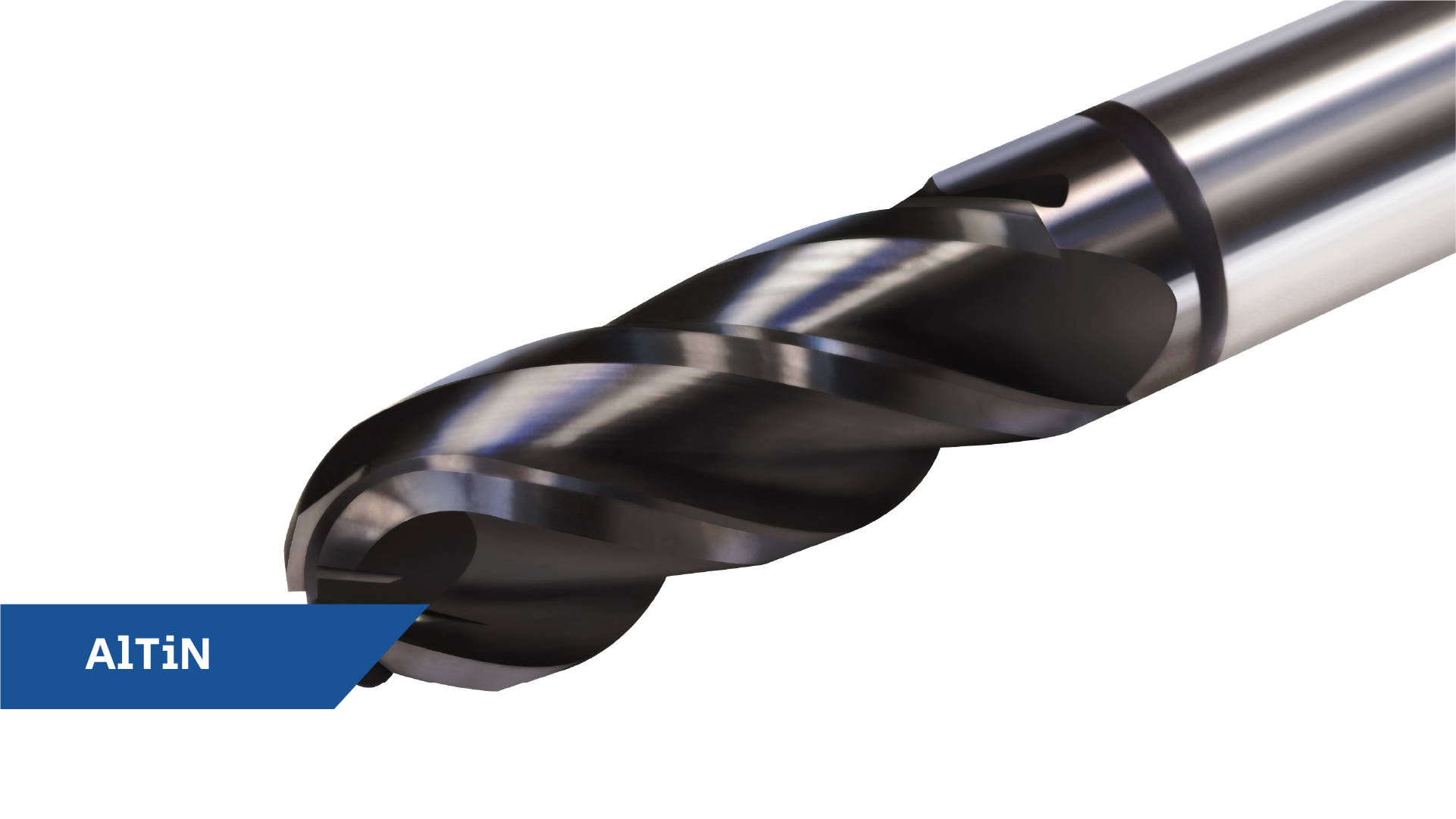
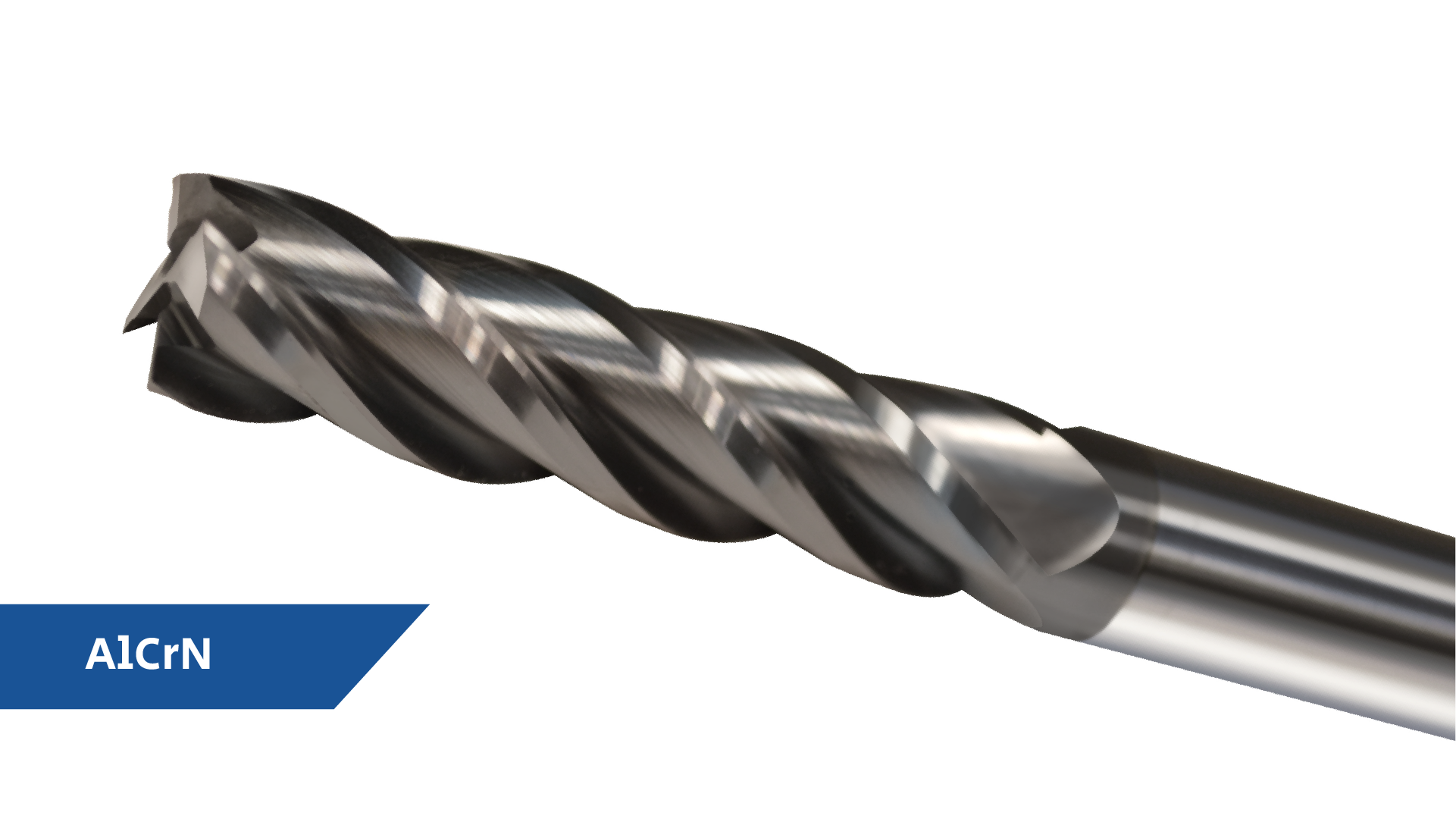
Aluminum Chromium Nitride (AlCrN)
Aluminum Chromium Nitride (AlCrN) is a PVD Coating with a Blue Grey color. It is, particularly, designed to be adaptable for multiple applications. This coating is tailored to combat common industry headaches, from erosion to high compression and high temperature production processes.
The AlCrN coating exhibits excellent toughness, at an extremely high temperature. Not only that, this PVD Coating will provide wear resistance under extreme conditions, such as mechanical stress. It can, additionally, be utilized on tools that are for working gears, cylinders, stamps and forms. This PVD coating is highly dedicated to the treatment of hard-to-cut materials.
Oftentimes, our coatings can be removed without finish degradation, then reapplied easily. With professional, experienced Engineering Technicians and tribology laboratories, we can precisely create solutions that will assist you in choosing the PVD Coating process best for your company’s manufacturing needs.
LET’S GET STARTED.
Ready to find the perfect tool, machining or PVD coating solution? Get started today.